Regardless of the aesthetics of what I’m building my first priorities are sound and playability. I work a little bit different from most guitar makers in that if there is a “feature” I believe improves the functionality or performance of an instrument it just becomes “standard”. Considering the time and effort involved in the crafting of a concert instrument I feel like I owe it to myself to build the very best instrument I can.
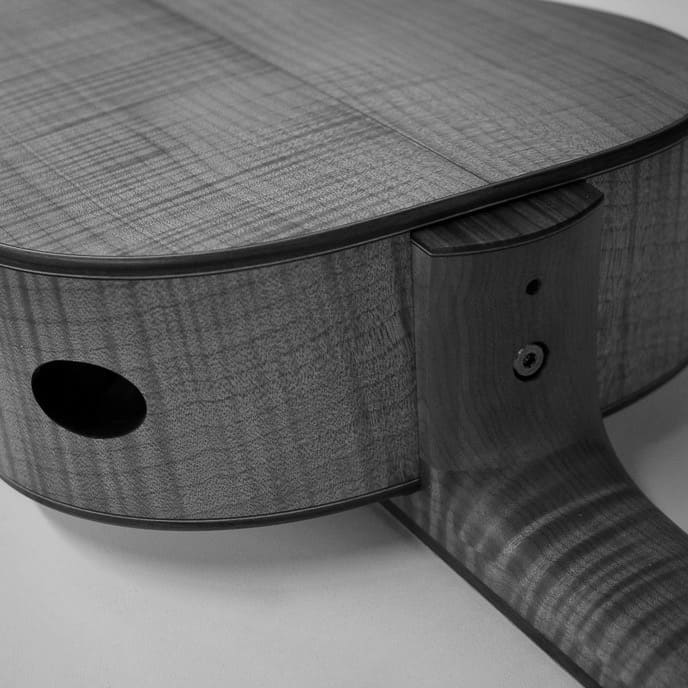
Adjustable Neck:
Commonly seen on instruments from the 19th century, the idea of an adjustable neck is not a new concept. I have adopted the adjustability based on my experience with the dichotomous needs of concert players. In the first regard, the ultimate in sound, sensitivity and responsiveness from their instrument, and in the second, the ability to optimize the action to compensate for different playing needs and for humidity variations. Adjusting the neck for your ideal playability requires a common hex key and a moment of your time.
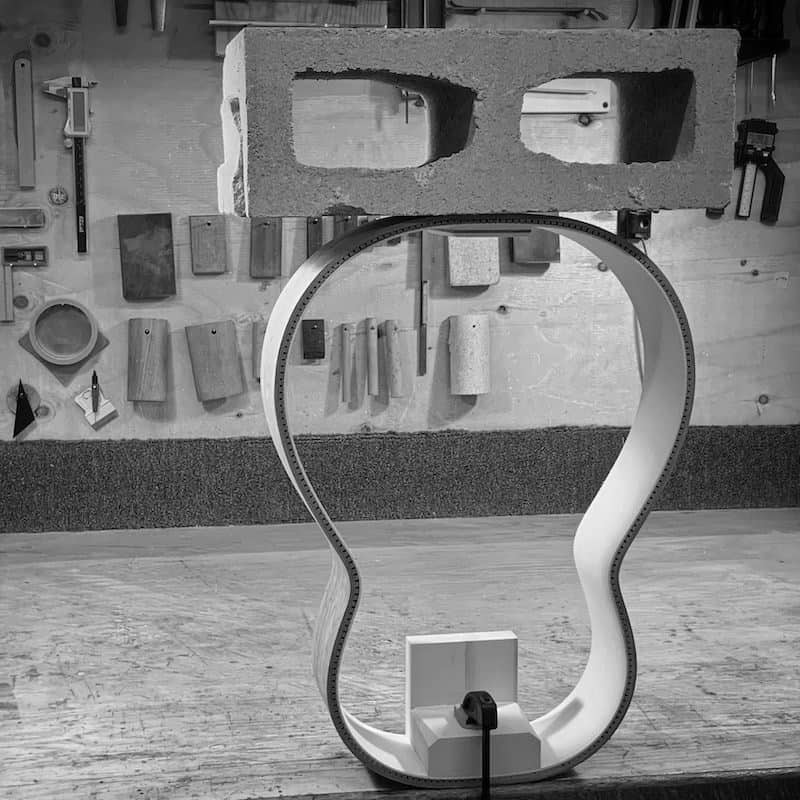
Structured Sides:
The “output” of a guitar is directly related to how much of (and how efficiently) the top is being "used”. Minimizing losses to the system and ensuring that as much of the potential energy possible is contributing to the production of sound is fundamental. Increasing the stiffness of the perimeter allows me to transfer the structural load on the top (due to the string tension) into the sides and establishes a dramatic reduction in inherent stress. Freeing the top from that stress allows me to simplify the intention of its structure to maximize the potential for sound production. In many ways the weight of the perimeter matters just as much as the stiffness. When you examine the node lines of the primary resonant frequency of the top of a typical guitar they are (usually) somewhat “inboard" of the perimeter. Adding mass to the sides shifts the node lines closer to the perimeter (i.e. more of the top working in phase) demonstrating the reduction in the movement of the guitar body and an increase in the movement of the top. More movement directly equates to more sound.
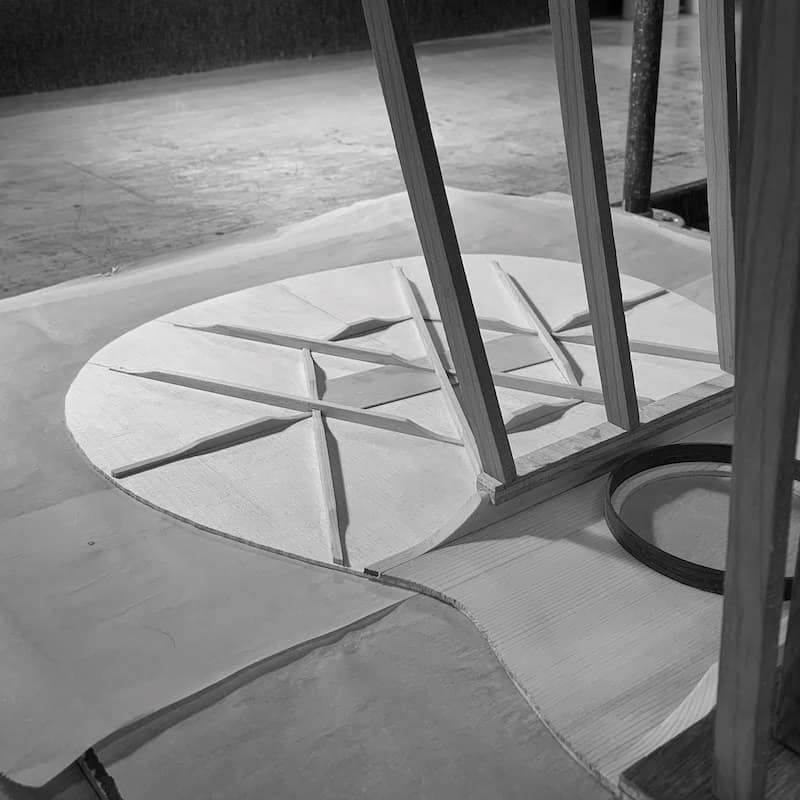
Hex Bracing:
Few elements of construction have obsessed me more than bracing. I have built with or tested hundreds of patterns. Traditional (and non-traditional) fan patterns, lattice patterns, radial patterns, and a multitude of other variants. I tend to view the top braces not only a structural component but also as a system to influence movement. “How” the top moves is an incredibly critical component to the quality of the instrument. Balancing those movements and controlling which frequencies they present at contribute to the voice and overall efficiency of the soundboard. Several years back I devised a bracing pattern based around the idea that the triangle is the most basic self stabilizing polygon. Six equilateral triangles around a vertex is one of the only entirely symmetrical/stable least-effort structural systems in nature. The evolution of my initial idea has developed into a single hexagon supporting the bridge area that is then "tethered" to the perimeter. It’s a beautiful distribution of stiffness that yields an impressive monopole mobility (more movement equates to more sound) and gives me the ability to manipulate the top in ways that I really like. The resultant instruments have a voice that is impeccably balanced, beautifully articulate, richly colourful, and powerful enough for the most demanding of halls.
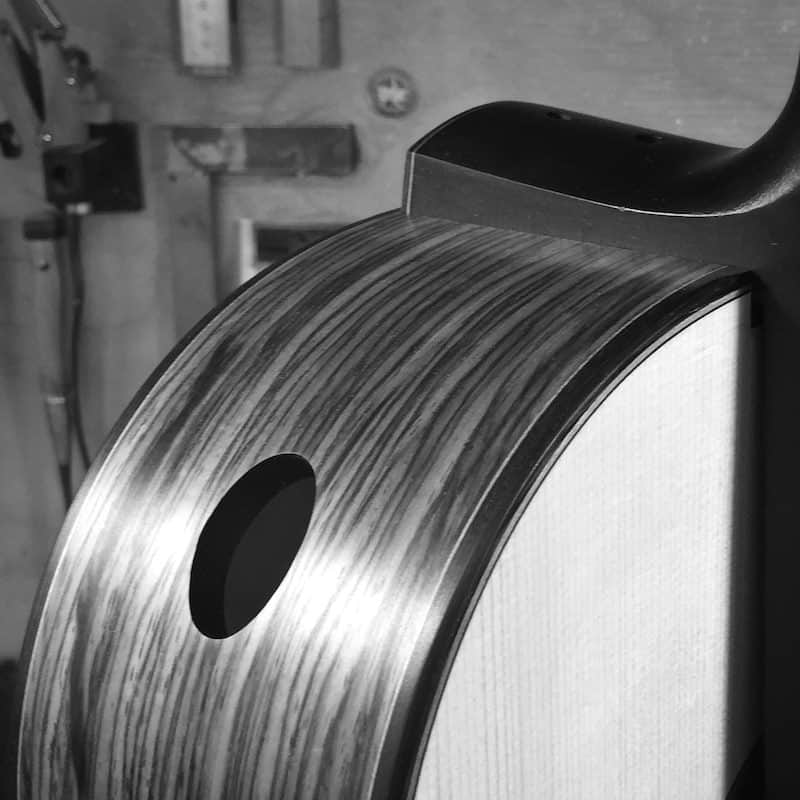
Sound Port:
The “output” of a guitar is directly related to how much of (and how efficiently) the top is being "used”. Minimizing losses to the system and ensuring that as much of the potential energy possible is contributing to the production of sound is fundamental. Many players (and makers) view the sole purpose of a sound port as that of a "monitor" for the performer. I think of it a little bit differently. I use a small port on the player's side for two primary reasons: adjusting the frequency of the air cavity and air exchange. Cutting a sound port into a guitar effects the resonant frequency of air cavity. Careful adjustments to the size and position of the port allows me to target a specific pitch and optimize the voice of the instrument. If you consider that the guitar is an incredibly complicated air pump the importance of moving air seems totally reasonable. Imagine trying to run a marathon with your nose plugged or pouring gasoline out of a jerrycan with the vent closed..."glug-glug-glug". Now imagine unplugging your nose during that marathon or opening a vent in that jerrycan... "whoosh". For guitars that "whoosh" is a very good thing.
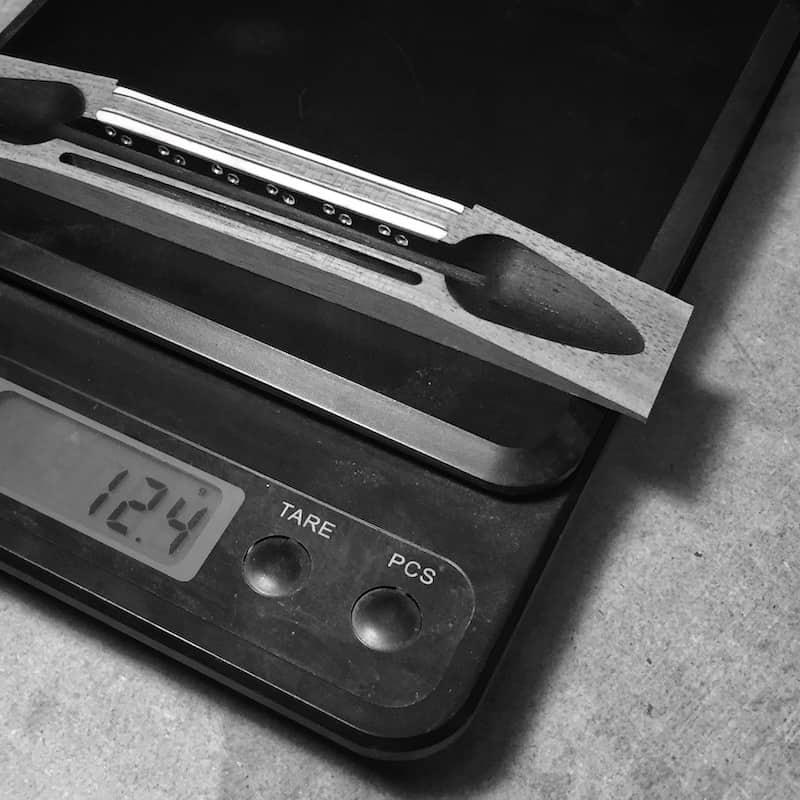
Low Mass Bridge With Reinforced String Holes:
The bridge of the guitar is the single heaviest "brace" on the top. The acceleration of the bridge is directly related to the production of sound —more acceleration equates to more sound. Lower mass bridges accelerate more under the oscillatory force of the strings. My bridges are exceptionally low mass and shaped for strength and stiffness. I believe that as guitar makers it is our responsibility to pursue the exploration and development of our instrument. Honouring tradition means respecting what works and correcting what history has told us is flawed. Over time the string holes in the bridge will distort due to the crush of localized loading, so I install metal bushings in my string holes to ameliorate the issue.